In the early 90’s, we had an inventor come to us and ask for a seal. It had
a very thin wall that had to maintain concentricity in order to work properly. Not
a big problem, until his product took off and the requirements went to 1.5 million
per month. Our toolmakers responded and we built one tool that could handle the
volume and maintain the accuracy required. High cavity tools give long tool life.
|
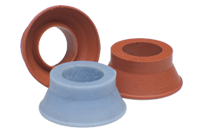 |
|
In this part, the customer was faced with the problem of having to get each drip
to have ‘exactly’ the same volume in a drop of water through the ID
hole on all parts from all cavities on a 1000 cavity mold. Flash and variations
would normally be a problem. Our toolmaker found a way to make no flash or parting
line on the inside diameter. This part ran 11 million parts a year for 8 years on
one mold. |
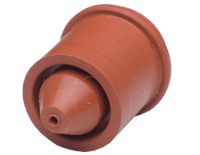 |
|
In this example, 3 parts were combined into one for the customer and in the process,
saved tooling expenses and eased assembly. |
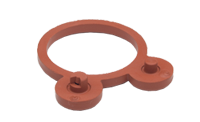 |